We are already living in the future. Watch any old movie and the “futuristic” technology they talk about is at our fingertips every day.
The technological revolution we’re experiencing is disrupting the business landscape. Nowhere is that more true than in the manufacturing industry. Facilities managers around the globe are leveraging the power of automation and RPA on their shop floors.
Automated guided vehicles (AGVs) are a key part of this push toward automation. These vehicles can accomplish most of the tasks warehouse workers have been doing for decades.
The result is a more efficient, productive facility. Team members are also able to focus more of their time and energy on high-value tasks instead of mundane menial labor.
Today, we’re going to talk about AGVs in-depth. We’ll discuss how they’re changing the face of an industry and then compare them with autonomous mobile robots (AMRs).
Stick around with us until the end. There’s a lot to learn!
What Are Automated Guided Vehicles (AGVs)?
AGVs are a more modern solution to performing day-to-day tasks on a facility or warehouse floor. These vehicles are essentially robots. They can move around the shop floor on their own.
These vehicles are also equipped to handle heavy lifting. Warehouses all over the country are using AGVs to move inventory from location to location within their warehouses. These robots can even be helpful when it comes to loading and unloading shipments.
AGVs navigate similar to a train. They follow “tracks” that are laid out with magnetic tape on the warehouse floor. Once a track is laid down, AGVs can’t move off of that track.
The only way for AGVs to move in another direction, or to another location, is to pull up the tape and lay it down in a different pattern. AGVs also lack the ability to avoid obstacles. It won’t run into things, but if an obstacle is present, the AGV will stop and wait for the obstacle to be removed from its path.
AGVs are an effective solution to help increase manufacturing productivity. But, they do lack some mobility and flexibility. Nevertheless, they are an amazing innovation to the warehouse workflow.
AGVs also laid the groundwork for their more modern successor, the AMR.
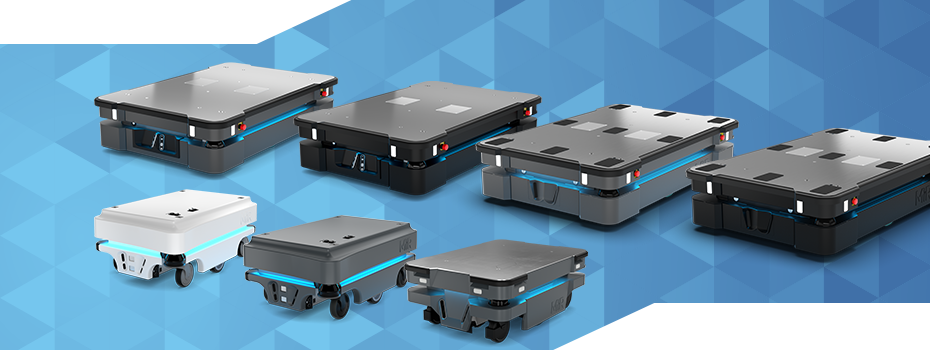
What Are Autonomous Mobile Robots?
AMRs are similar to AGVs. They are robots that can assist with the daily operations of the warehouse workflow. The biggest change between an AMR and an AGV is that AMRs are equipped with natural navigation.
This means that AMRs are smarter. They’re not confined to a track of magnetic tape. They can “think” for themselves and follow the fastest route from point A to point B.
This means that if an AMR encounters an obstacle, it can navigate around it. It doesn’t need to wait for assistance from warehouse staff to remove the obstacle.
These machines are also rated for heavy weight limits. AMRs can navigate around the warehouse floor while carrying thousands of pounds in inventory to their appropriate destination.
With more intelligence comes more data and analytics. The result is an autonomous “employee” that gives warehouse managers incredible insight into the daily operations of their shop. The analytics and reporting AMRs can provide offers opportunities to improve processes and optimize your shop’s performance.
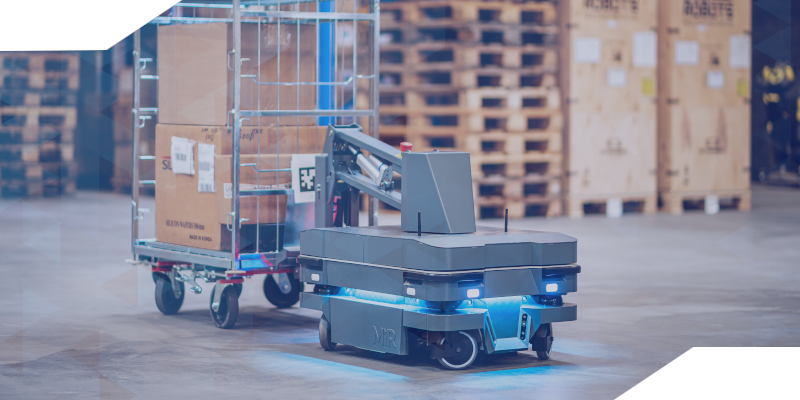
AGVs vs AMRs
Since AGVs gave birth to AMRs, both terms wind up getting used interchangeably. It’s easy to get the two confused because there are a lot of similarities. But, there are also some major differences.
Let’s take a detailed look at where they’re the same, and where they differ, down below.
Similarities
The first thing they have in common is their role on the shop floor. Both of these machines can move inventory, equipment, etc. around the shop floor. Both AGVs and AMRs can handle very heavy loads. Think of them as forklifts with minds of their own.
The next major similarity is that both robots are “smart” enough to avoid collisions with objects. As long as you keep objects clear of the magnetic tape used with AGVs, you should be good to go. This leaves factory workers to focus on more high-value tasks that can only be done by human team members.
Differences
AGVs and AMRs have more differences than similarities. Both are effective when used in the right circumstances, but AMRs have more functionality in the workplace.
AGVs can be a great solution for smaller operations. Their controls are much simpler to use. They can also be much cheaper than their AMR counterparts.
AGVs can also handle large payloads like airplane engines and train parts. The challenge with AGVs, however, is that they aren’t “truly” autonomous.
Since AGVs rely on sensors or magnetic tape to move, it can sometimes present challenges for warehouse operations. Once a path is laid out for an AGV, they can only move along that path. In order to change the path, warehouse staff needs to stop what they’re doing and re-lay the magnetic tape or reset the sensors.
This means that warehouse shelving needs to be designed and laid out in a certain format to accommodate AGVs. AMRs don’t require that kind of planning.
With AMRs, warehouse managers can choose to layout their factory floor in the way that best suits them and their operation. They don’t need to worry about accommodating machinery like AGVs.
AMRs are the first type of equipment to navigate in a “truly” autonomous fashion. They are simply programmed with a starting point and endpoint. The rest is up to them.
They will find the best way to get between the two points without any help from human team members. They also can follow a person around the warehouse floor by using a “follow me” command.
One of the downsides of AMRs is that they can get “lost” if they follow too complex of a route around the shop floor. But, they can also work outside of your building since they communicate over the cloud.
They’re not perfect yet, but AMRs are an overall net positive so far.
Johnny Five Is Alive
Automated guided vehicles and mobile robots are revolutionizing the manufacturing and distribution space. AGVs have been around for decades, but AMRs are just coming onto the scene. Thanks to AI and machine learning, warehouse staff can focus on finding solutions to complex projects that are actually worth their time.
If you have any questions about AMR technology, contact us today. We’d love to help you leverage automation to bring your operations to the next level.
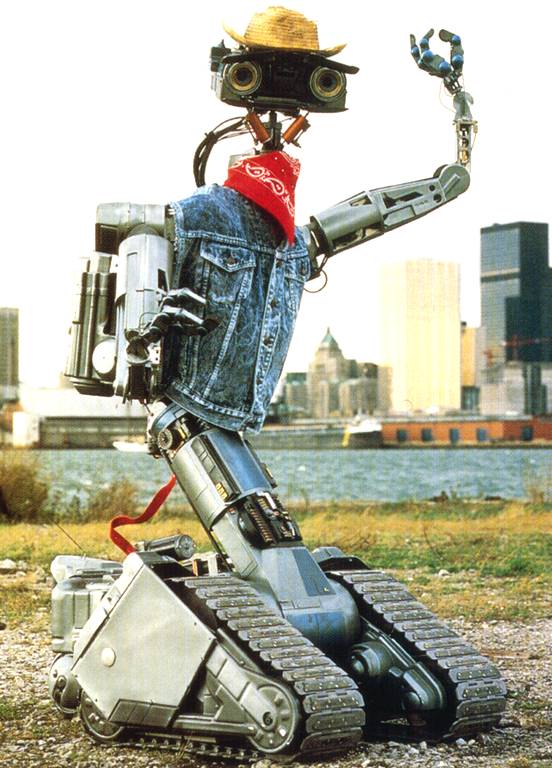
Recent Comments